Home
Main content starts here, tab to start navigating
Stir-fry, Salad, Honeybar Specialists Since 2012
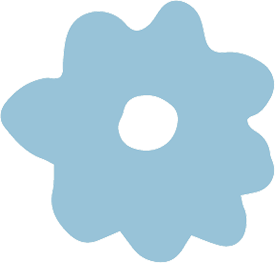
Your event is about to get a whole lot more delicious
hg catering
Who doesn't like free food?
join our rewards program and start earning points today
Click to Join